Why we need your walls and your floors
It helps us help you.
A successful window installation is partially contingent on understanding the building materials and design elements chosen for a particular project. Factors such as where and how we install a window in an opening will depend on:
Wall types and cladding types - for example, brick, stucco or siding.
Drainage paths of walls - walls all must deflect water towards the exterior of the facade. Some walls deflect water in a plan closer to the interior of the wall, some closer to the exterior of the wall.
Where the main control layers for temperature and vapour reside.
Different walls have different drainage paths.
Take the above window head details, using the exact same CS 77 Outer frame. You can see that the drainage paths vary by 1.15” depending on the selected wall types for the project (6” Forward from back of wall framing @ Fig.3, 7.15” From back of wall framing @ Fig. 1).
Where the window sits in the opening must relate to drainage paths - if your window is situated exterior relative to the drainage path, the water management of that penetration is hindered. If the window is situated to close relative to the interior, there will be some cosmetic issues with exterior finishes - who wants to cap out brand new windows with trim coil on a brand new luxury custom home?
The main takeaway here is: We need to know what your wall make up is for your project to determine where the window sits in the opening. This will set the stage for interior and exterior finishes.
Different floors have different thicknesses - don’t you want your door to swing?
Conventional size approvals for windows and doors usually dictate that rough openings are 1” greater in height and width than frame sizes. In other words, your window or door sill, head, left and right jamb each have a half inch of space for levelling, and foaming.
Take a look at the 2 drawings below. With drastically different flooring makeups and installation conditions, the sill details are completely individual to the conditions of each project - In any case, the conventional 0.5” of spacing would not facilitate door operation - meaning other trades coming in after window and door install would have to make some shifts in their plan. We want to ensure that the drawings are being respected and followed, and we want to ensure trades responsible for interior and exterior finishes are able to complete their portion of the project without any surprises or contingency.

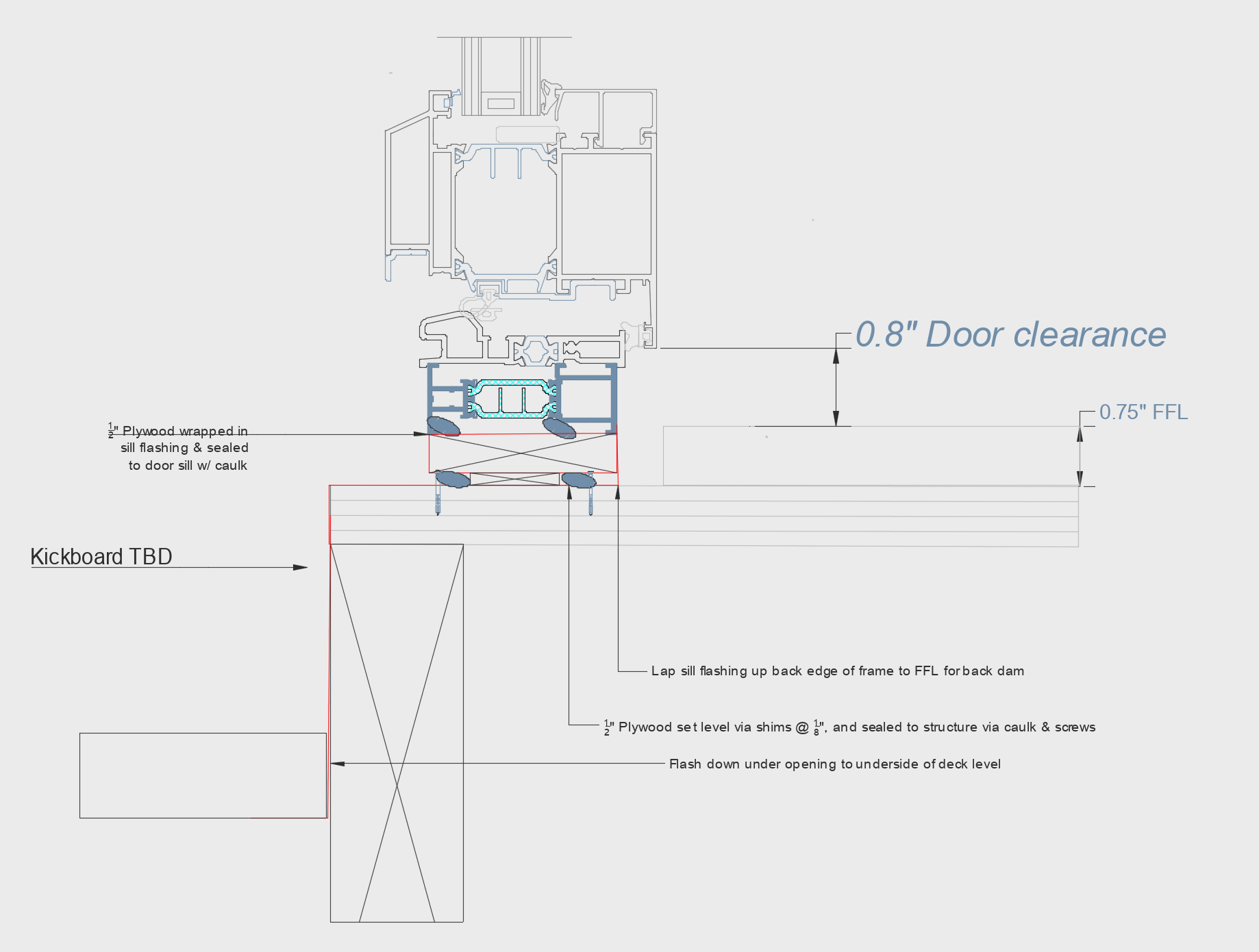
The main takeaway: Ample door clearance serves as a main concern when reviewing installation plans. Knowing floor thicknesses helps us determine how we can ensure an air and watertight door installation that passes on easy functionality to the end user.
It keeps everyone on the same page. No room for guessing!
By using the specified wall and floor details in approved construction drawings, we are able to pinpoint exact variables relating to design and performance in respect to window installation for the specific project. A set of approved drawings dictate exact specifications for structural, thermal and water shedding applications, therefore serve as the ultimate frame of reference for successful window and door integration. We will always strive to follow what is signed off on and approved, and make the assumption that all other trades do as well. Otherwise, whats the point of even having a set of construction drawings?
There is no guesswork required when you do what you say, and say what you do.
Questions about an upcoming project?