Going beyond the rough opening: How we spec your windows and doors for high performance installations
I’d like to address some common misconceptions pertaining to window installation, and some things we have learned through our experience:
It’s not just about fitting a window in a rough opening
It’s difficult to convey this to end users (homeowners)
It can be even more difficult to convey this to trades (surprisingly)
What happens after a window installation can mean all the difference between high performing facades, clean finishes, vs. leaky windows with cheap finishes.
This is why a project isn’t just any other project, aka another opportunity to supply another lift and slide, or glaze another floor to ceiling unit. It’s an opportunity to collaborate with thoughtful and talented teams to create something meaningful and valuable. Our main goal as a window and door supplier is to lend to the practicality in design and functionality that homeowners dream of, architect envision, and builders execute on.
We understand the collaborative approach required for building beautiful, contemporary spaces.
We obsess over details relating to thermal performance, water tightness, and end user utility.
We aim to simplify the window and door procurement process.
Platitudes such as ‘expanding your view’, ‘pushing the bounds of architecture’ and ‘minimal frames’ can become smoke and mirrors meant to ooh and ahh designers that distract from the real value a high performing aluminum window and door system offers - high performance, ease of use, and yes, thin frames (but probably not as thin as you think) - only when considered within the context of specified building methods and selected materials.
In other words:
What good is your door if it can’t swing past your finished floor level, because no one bothered to double check the tile being ordered was true to spec on the construction drawings?
Is the extra 0.5” in sightline saved worth the bowing window frame, and window operable that now never closes?
Let’s take a look at the following case study - a front door replacement project - which gave us the opportunity to exercise full control over the surrounding components of installation to ensure complete air tightness, thermal continuity, and a product that works with finishes, and above all, looks good!
What goes in a successful window & door replacement
In retrofits, its often difficult to assess what the rough opening conditions are underneath existing window frames - there’s no telling if the window bucks are in fantastic condition, there is no telling where the house wrap is located, and what the thickness of the floor is. Luckily, in this situation, the builder who completed the front addition several years ago was around and we were able to get these details from him.
The approved header detail for this project. Note that removal of perimeter finishes is specified for building paper exposure.
Recreating a continuous air/vapour barrier
The purpose of an effective air barrier is to regulate the indoor climate by stopping the transfer of air, and the moisture associated with, between the interior and exterior of a home. An air barrier must also resist air pressure differences that act on them. Interruptions in the air/vapour barrier mean exposure to risk of climate dis-regulation and moisture accumulation in the walls, aka less efficient walls and mold.
Window openings are ‘penetrations’ in the continuous air/vapour barrier that the house wrap and interior vapour barrier. So are pipings, electrical work etc.. however, windows and doors present themselves as the largest and most significant penetrations in the continuous barrier. It’s why there is a sequential process to installing windows in a new build - so that all measures of thermal performance such as vapour barrier connections at penetrations, along with proper head and sill flashings, can be completed without obstruction from finishing elements. We don’t have that luxury with a retrofit, since, well, the house is already built. We can, however, emulate new build conditions to the best of our ability around the perimeter of the rough opening so that our replacement is a replacement and not a patched up hackjob.
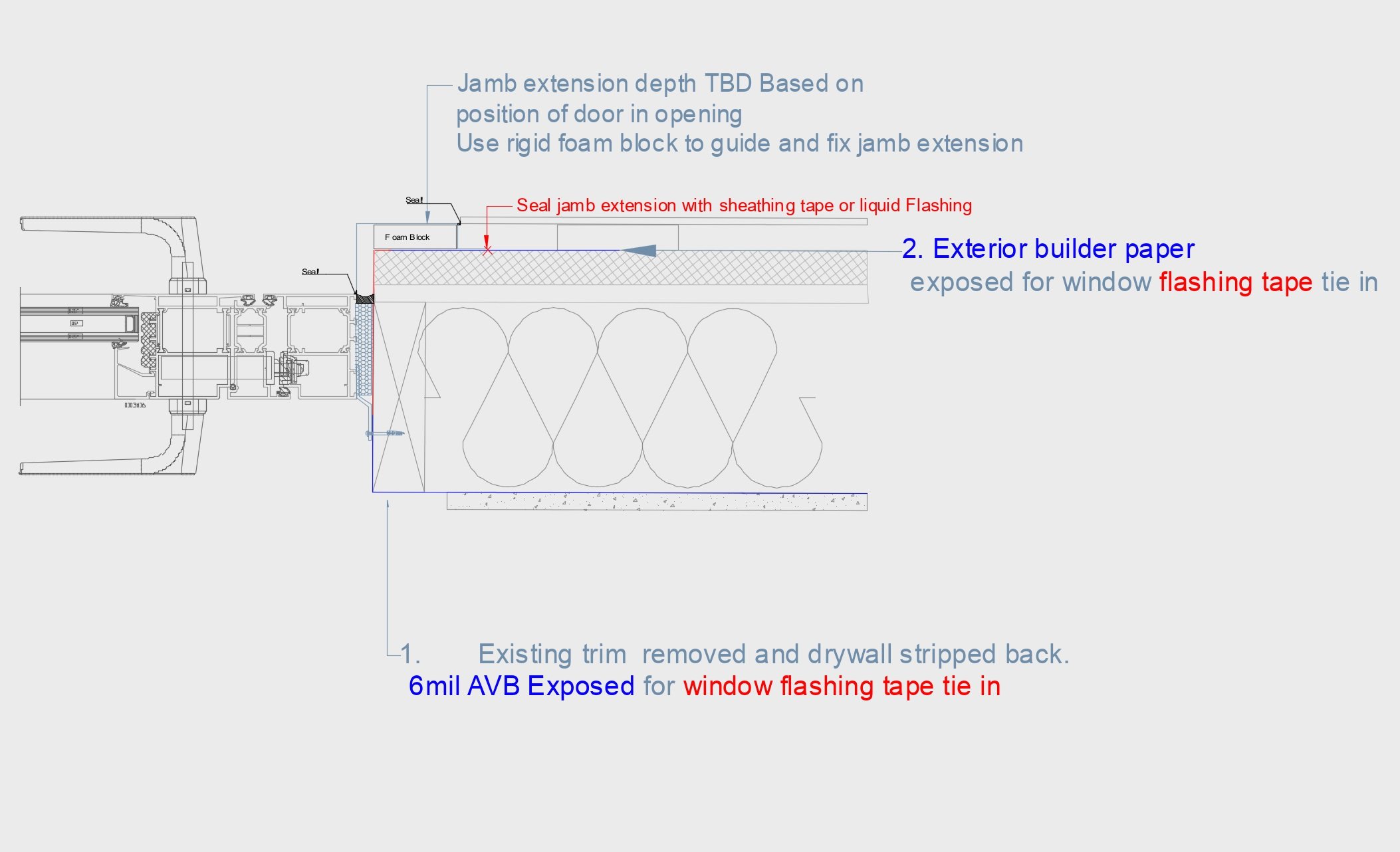
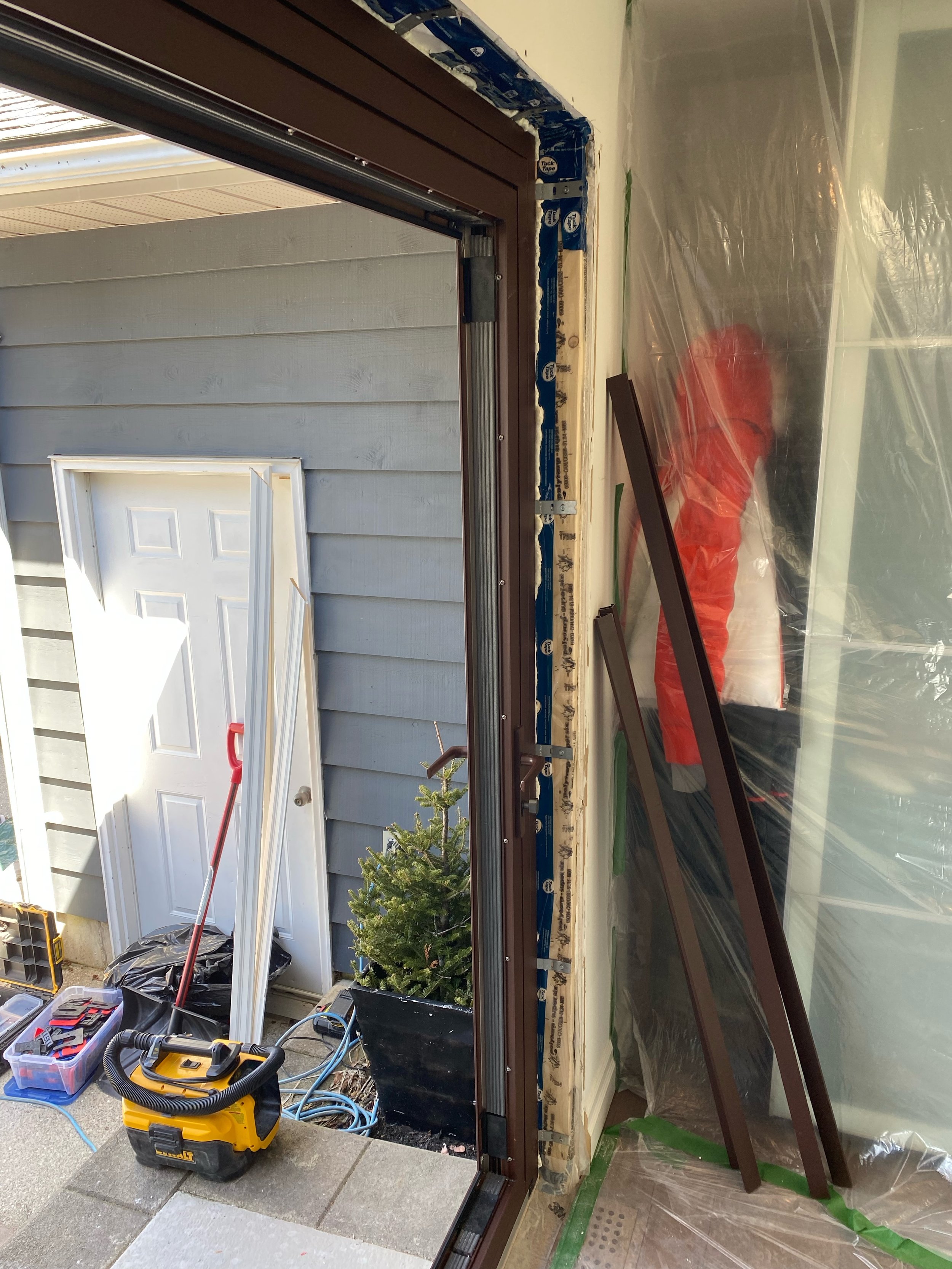
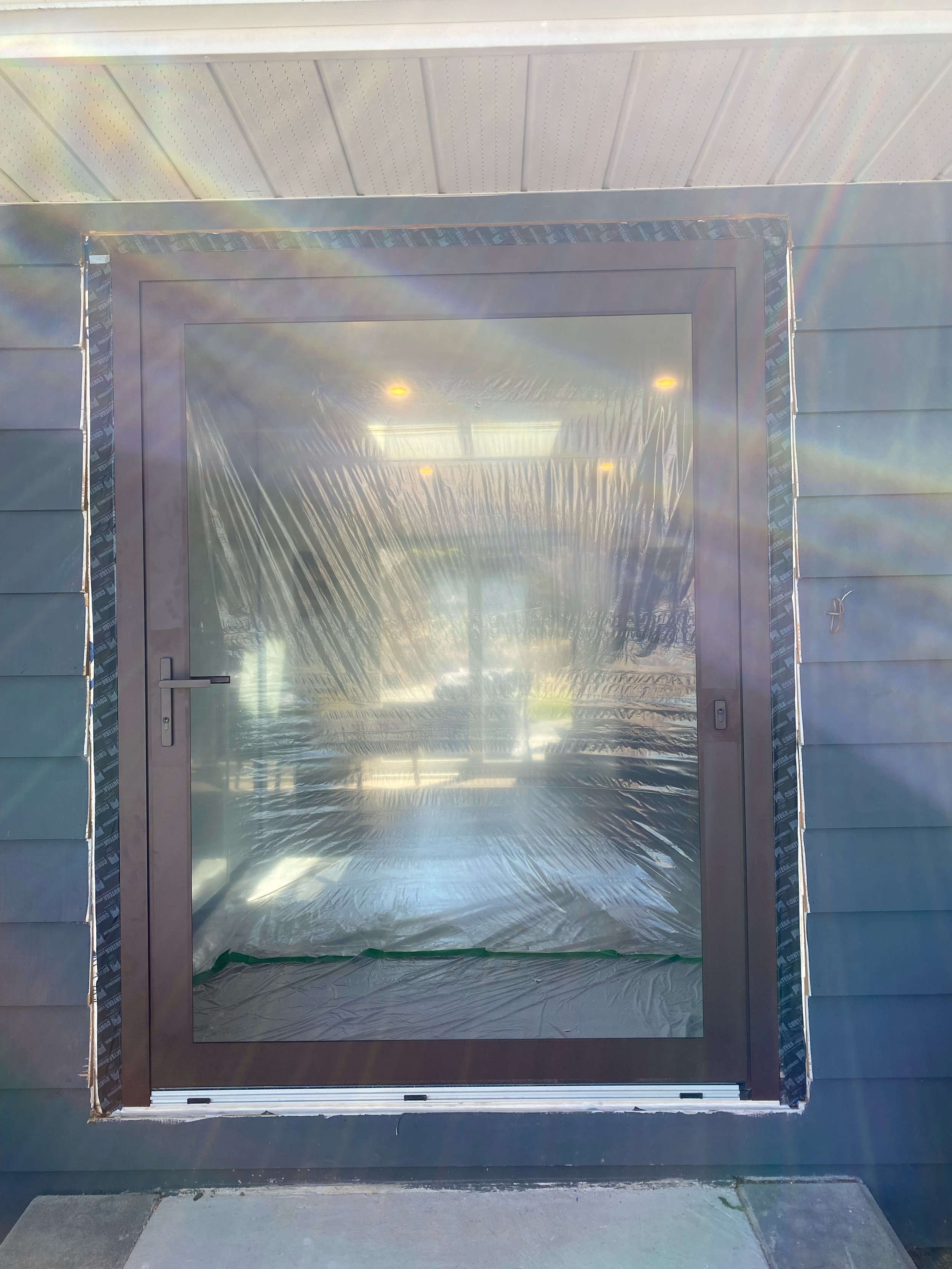
Conclusion
There is more to a window installation than fitting a window or door into a structure and foaming the perimeter
The wall types need to be understood, so that installation allows for proper exterior finishes, drainage, and interior swing clearance (for doors and floor to ceiling windows)
Retrofits run the risk of creating disruptions in the continuous air and vapour barrier. A window retrofit job is really a retouching of all construction elements around the penetration in the wall. Expect the need for trades to work on drywall, drainage and head flashings, and sometimes flooring.
Gutting a house? get in touch with us to discover how we can help with your high performance renovation.